Modbus protocols are crucial components within industrial automation & control systems. Designed in 1979 by Modicon, Modbus emerged as a means to facilitate communication among Programmable Logic Controllers (PLCs) and different devices within industrial networks. Over time, the protocol underwent evolution, becoming highly adaptable and gaining popularity across diverse industries, primarily through the prominence of RTU and TCP protocols.
Table of Contents
- Overview of Modbus Protocols
- Modbus RTU vs Modbus TCP/IP
- An Overview of Modbus RTU
- Modbus RTU Frame Structure
- Modbus RTU Error Detection
- An Overview of Modbus TCP/IP
- Modbus TCP Frame Structure
- Modbus TCP Error Detection & Correction
- Communication Media & Speed (Modbus RTU vs Modbus TCP)
- Cost Considerations (Modbus RTU vs Modbus TCP)
- Network Security (Modbus RTU vs Modbus TCP)
- Ease of Integration (Modbus RTU vs Modbus TCP)
- Network Topology & Scalability (Modbus RTU vs Modbus TCP)
- Real-World Applications
- Conclusion
- FAQ
Overview of Modbus Protocols
Imagine scenarios where monitoring & controlling multiple freezer temperatures across hospital floors, managing devices at home, tracking traffic patterns, or overseeing diverse industry stations’ devices is crucial. The Modbus protocol simplifies these tasks enabling easy & centralized management.
In simple words, Modbus designers created it to facilitate seamless data transmission among electronic devices. Its significance lies in industrial applications where quick decisions rely on analog data from sensors utilized by industrial computers, PLCs and SCADA systems. Fortunately, most industrial devices support the Modbus protocol.
As an open-source protocol, it’s freely available online for download, making Modbus the go-to standard in the control and automation industry. The implementation occurs in various sectors such as oil, gas, wind, solar, and more. Streamlining data transfer within a single layer, it excels at tasks like gathering analog data from sensors, unifying monitoring on a single interface & facilitating communication among industrial and automation devices.
Modbus RTU vs Modbus TCP/IP
Modbus RTU (Remote Terminal Unit) and Modbus TCP (Transmission Control Protocol) are the most commonly used Modbus protocols today, although various others exist. These protocols are all appropriate for different environments and use cases due to their unique features, benefits & applications. Modbus data efficiently flows through two main channels: the Modbus serial (via RTU) and the Modbus Ethernet layer (using TCP protocol).
Modbus RTU is perfect for systems that need simple, secure & affordable communication since it uses serial communication to transfer data between devices. Applications including industrial process control, building automation, and remote monitoring frequently make use of Modbus RTU.
On the other hand, Modbus TCP uses IP & Ethernet networks for communication, allowing for greater scalability and speed in more complex and demanding environments. Applications requiring high-speed communication, like data center administration, oil and gas production and power generating frequently use Modbus TCP.
The main focus of this blog will be an analysis of Modbus RTU vs. TCP using a variety of technical and practical details, including a comparison of the communication & network frameworks, security issues, financial considerations, real-world applications and more. You will have a thorough grasp of these two industrial protocols by the end of the discussion & you will be able to select the one that best suits your needs.
An Overview of Modbus RTU
The most popular industrial communication protocol is Modbus RTU (Remote Terminal Unit), which exchanges Modbus data using serial communication for data exchange between devices. Systems requiring reliable communication but not fast data transfer are attracted to it because of its affordability, dependability, and simplicity. Industrial process control, remote monitoring, and building automation are a few typical application areas for Modbus RTU.
The Modbus RTU protocol operates across multiple physical layers such as RS-232, RS-422 and RS-485 (where RS stands for Recommended Standard), allowing it to meet varied communication needs. RS-485 supports multi-drop configurations and communication distances of up to 1,200 meters, making it the most widely used implementation. Modbus RTU can achieve varying maximum data rates depending on the physical layer used. For example, RS-485 is capable of speeds up to 10 Mbps.
Modbus RTU Frame Structure
The Modbus messaging frame structure for RTU facilitates communication between devices and ensures efficient data organization and transmission. Within these frames, every field has a unique function:
Address Field
The address of the device (slave) for which the message is intended is contained in this one-byte field. Through repeaters, a single network can support up to 247 devices with addresses ranging from 1 to 247.
Function Code Field
This 1-byte field specifies the kind of operation such as reading or writing data that the slave device is to carry out. Function codes range from user-defined (128-255) to standard (1-127).
Data Field
The information that must be transmitted between devices is contained in the data field. The size varies (up to 252 bytes) based on the function code and the amount of data engaged in the operation.
CRC (Cyclic Redundancy Check) Field
To detect errors & guarantee data integrity during transmission, the two-byte CRC field is utilized. Except for the CRC field itself, it is computed using the contents of the full frame.
A standard Modbus frame starts with a silent interval of at least 3.5 times the period of a character, followed by the address field, a function code field, a data field & finally the CRC field. The frame ends with another silent interval of a comparable length following the CRC field.
The data in Modbus (both RTU & TCP) is stored in Modbus registers, which are memory locations for storing different types of data, floating-point, integer, binary, custom data types, etc. In Modbus, the registered address has a range of 0 to 65,535. Coil, Discrete Inputs, Holding registers & input registers are the most often used Modbus register types.
Modbus RTU Error Detection
Modbus RTU uses Cyclic Redundancy Check (CRC) for error detection, ensuring data integrity. CRC detects various errors, including single-bit and burst errors, by calculating a remainder from the frame’s content (excluding the CRC field) using a predefined polynomial. This remainder is added as a 2-byte CRC at the end of the frame.
The receiving device recalculates the CRC and compares it to the transmitted value. If they match, the message is processed; if not, it’s discarded, and the sender may be asked to resend it. While CRC is not foolproof, its effectiveness in detecting errors makes it a reliable method for Modbus RTU in industrial applications.
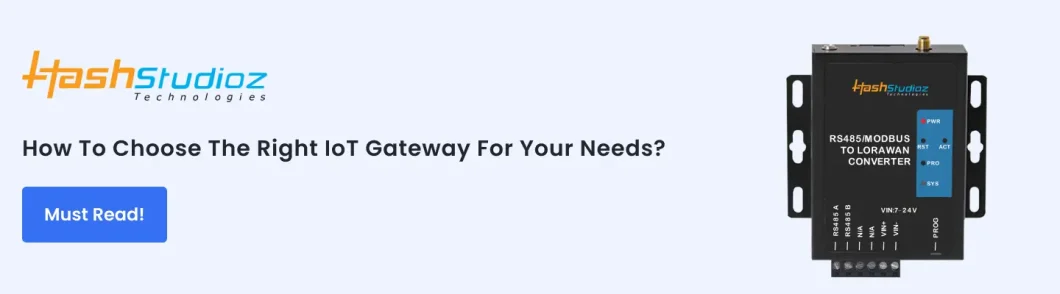
An Overview of Modbus TCP/IP
Modbus TCP/IP (Transmission Control Protocol) is an adaptation of the Modbus protocol designed for communication across Ethernet & IP networks. As industrial networks have become more complex & demanding, Modbus TCP has emerged as a popular choice for applications requiring high-speed communication & higher scalability.
Modbus TCP preserves the simplicity & ease of use associated with the original Modbus protocol while taking advantage of the benefits offered by Ethernet and IP networks. It offers increased data rates, improved network reliability & the ability to connect more devices compared to RTU. Also, Modbus TCP may make use of already-existing Ethernet infrastructure which minimizes the need for specialized hardware & streamlines network setup.
Modbus TCP Frame Structure
The Modbus messaging frame structure for TCP is made to facilitate communication over Ethernet and IP networks. Modbus TCP adds more fields to meet the needs of Ethernet & IP connection, even though it shares similarities with the Modbus RTU frame in certain ways. The following fields make up a Modbus TCP frame:
MBAP Header
Exclusive to Modbus TCP, the Modbus Application Protocol (MBAP) header is a 7-byte field. It has all the data required for the message to be routed & processed in an Ethernet and IP environment. There are four subfields in the MBAP header:
- Transaction Identifier (2 bytes): This field matches a request message with its corresponding response message.
- Protocol Identifier (2 bytes): When Modbus communication is enabled, the system always sets this value to 0, indicating the use of the Modbus protocol.
- Length Field (2 bytes): This field specifies the number of bytes left in the frame excluding the MBAP header.
- Unit Identifier (1 byte): This field contains the address of the device (slave) to which the message is intended, similar to the address field in Modbus RTU.
Function Code Field
Similar to Modbus RTU, this 1-byte field specifies the kind of operation such as reading or writing data that the slave device is to carry out.
Data Field
The data field contains the information that devices must transmit. The function code and the amount of data used in the operation determine its size.
To sum up, the MBAP header, function code field, and data field come first in a Modbus TCP frame.
Are you wondering what happened to the CRC field? Modbus TCP does not have a CRC field for error detection like Modbus RTU does since the underlying Ethernet and IP layers manage it.
Modbus TCP Error Detection & Correction
Unlike Modbus RTU, which uses CRC for error detection, Modbus TCP relies on the Ethernet and IP layers for this purpose. This eliminates the need for additional error detection at the application layer.
Ethernet Frame Check Sequence (FCS)
Ethernet frames contain a Field called the Frame Check Sequence (FCS). This FCS is a 4-byte value determined by using the CRC-32 algorithm. Just like the CRC in Modbus RTU, the FCS is computed from the frame’s data. Its purpose is to catch transmission errors. Devices handling Ethernet data discard frames that have incorrect FCS values, ensuring that only accurate frames get through for processing.
IP Header Checksum
A checksum field in the IP header allows for error detection within the IP header itself. The IP header’s 16-bit words are added, the one’s complement of the result is taken & the value is stored in the checksum field to compute the checksum. Recipient devices check the checksum of the IP header and reject packets with an invalid checksum.
TCP Checksum:
TCP employs a checksum to spot errors in both the TCP header and the payload and the IP header checksum. This process involves summing up the 16-bit words from the TCP header, payload, and a pseudo-header derived from the IP header. When the receiving device checks the TCP checksum and finds incorrect values, it discards those segments.
Retransmission
TCP includes methods to recover from errors like resending lost or corrupted segments. When a receiving device detects an error or doesn’t receive an expected segment within a set timeframe, it can ask the sender to resend the missing data. This mechanism guarantees reliable data delivery even when transmission errors occur.
Modbus TCP provides reliable communication & data integrity in industrial applications by relying on the error detection and correction methods integrated into the Ethernet and IP layers. By using this method, the Modbus TCP protocol can benefit from the stability and dependability of modern Ethernet and IP networks while also being made simple.
Communication Media & Speed (Modbus RTU vs Modbus TCP)
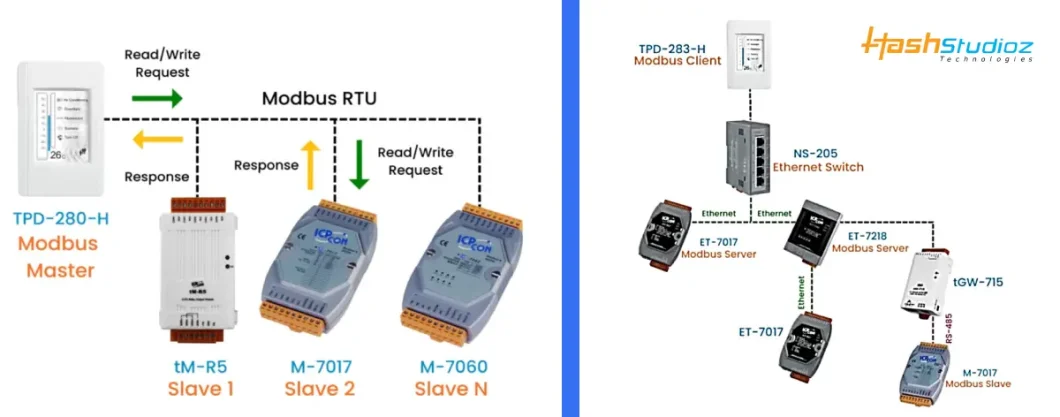
Modbus RTU Communication Media
Modbus RTU primarily relies on serial ports like RS-232 and RS-485. RS-232 suits short-range communication (up to 50 feet or 15 meters), while RS-485 supports longer distances (up to 4000 feet or 1200 meters) & facilitates multiple devices on a single line. It transmits data in binary format (0s and 1s).
Compared to Modbus TCP’s Ethernet-based communication, Modbus RTU’s serial communication is generally slower. RS-232 and RS-485 operate between 1.2 kbps and a maximum of 115 kbps, influenced by factors like cable length, noise & network device volume.
Modbus TCP Communication Media
Modbus TCP, using Ethernet, outperforms serial communication with higher speeds, improved reliability & broader industry acceptance. Ethernet’s versatility supporting various speeds and advanced features like QoS, enhances Modbus TCP networks, surpassing Modbus RTU’s speeds. Its reliance on Ethernet TCP/IP gives it an edge in communication speed and efficiency, making it increasingly popular despite RTU’s continued use in specific applications.
Cost Considerations (Modbus RTU vs Modbus TCP)
Modbus RTU Cost Factors
Modbus RTU is cheaper due to affordable hardware like RS-485, but may require more wiring and extras in larger setups. While it’s cost-effective for smaller systems, longer distances or noisy environments might drive up expenses for repeaters and shielding.
Modbus TCP Cost Factors
Modbus TCP needs pricier hardware like Ethernet switches and powerful devices, hiking up costs. Yet, its use of widespread Ethernet infrastructure can cut installation expenses. It shares communication channels, reducing dedicated wiring needs. Remote access cuts maintenance costs by enabling diagnostics and updates. Weighing hardware, installation & maintenance, and system designers can help pick the better fit between Modbus RTU and Modbus TCP.
Network Security (Modbus RTU vs Modbus TCP)
Modbus RTU Network Security
Modbus RTU is more secure against remote cyber threats due to its serial communication & physical access requirements. However, it lacks built-in encryption or authentication, leaving it vulnerable to data interception or manipulation if someone gains physical access to the line. To boost security, consider adding encryption or access controls.
Modbus TCP Network Security
Modbus TCP, based on Ethernet and IP, faces higher cyber threats than Modbus RTU due to its wider accessibility. It lacks native encryption or authentication, making data vulnerable to interception or manipulation. To secure Modbus TCP, use VPNs for encrypted communication, segment networks, employ firewalls & update devices regularly. Modbus RTU benefits from serial communication’s inherent security but lacks encryption, exposing it to physical breaches. Choosing between them depends on system security needs & the ability to bolster security measures.
Ease of Integration (Modbus RTU vs Modbus TCP)
Modbus RTU Integration
Modbus RTU, a serial protocol, easily fits into systems using RS-485 or RS-232. It’s great for older setups, offering simplicity that keeps costs down. But in larger systems, it can be tricky due to needing dedicated channels and facing signal problems in noisy or distant environments.
Modbus TCP Integration
Modbus TCP suits modern Ethernet-based industrial systems due to easy integration with existing networks, allowing local and remote communication. However, it demands more power and memory, making it tricky for legacy or resource-limited setups. Modbus RTU is better for simpler implementations and cost-conscious setups, especially in retrofitting legacy systems. Overall, TCP fits well with Ethernet systems, while RTU is more adaptable to limited resources.
Network Topology & Scalability (Modbus RTU vs Modbus TCP)
Network Structure and Scalability in Modbus RTU
Modbus RTU networks can adopt various configurations like point-to-point, multi-drop or multi-point setups. The prevalent choice often gravitates toward the multi-drop arrangement where numerous slave devices link to a single master device on a communication line, similar to a daisy chain. This setup utilizes RS-485 communication, accommodating up to 32 slave devices (expandable to 247 devices) on a single line. However, only one slave can communicate at a time within this master-slave structure.
Yet, Modbus RTU encounters constraints in network expansion and complexity. Managing and troubleshooting become challenging as the device count rises, compounded by the impact of overall network distance on communication speed and reliability.
Network Structure and Scalability in Modbus TCP
Modbus TCP, built on Ethernet and IP, supports diverse network layouts (star, tree, ring, mesh), aiding adaptable network design. It handles up to 247 devices with unique IP addresses for easy management. This scalability, ideal for expansive industrial systems, outperforms Modbus RTU, especially as networks grow in complexity. RTU suits smaller setups, but TCP shines for advanced monitoring across numerous devices in expanding businesses. Our IoT gateway supports both RTU and TCP/IP. You can get in touch with us for more information.
Real-World Applications
Choosing between Modbus RTU and Modbus TCP depends on system needs. Here are their key uses:
- Hybrid Applications: A combination of RTU for local communication and TCP for wider networking and remote monitoring works well in larger industrial setups.to use RTU’s simplicity and cost-effectiveness locally & TCP’s networking prowess for broader connections.
- Modbus RTU in Industrial Automation: Preferred for its simplicity, reliability, and cost-effectiveness. It’s ideal for small-scale setups, like factory floors, controlling PLCs, sensors, and actuators in time-sensitive applications.
- Modbus TCP in Building Automation & Smart Grids: Best for networking and remote access, connecting HVAC, lighting, and security in building automation, or enabling real-time monitoring in smart grids for better energy management.
Aspect | Modbus RTU | Modbus TCP |
Communication Medium | Uses binary encoding via RS-232 or RS-485 | Utilizes Ethernet networks as communication channels |
Packet Structure | Binary data with slave address, function code, data & checksum | TCP/IP packets with IP addresses, port numbers & Modbus payload |
Speed and Data Transfer Rates | Effective for non-speed critical applications | Offers faster data transfer rates, suitable for real-time communication |
Addressing | Each device has a numerical address (1-247) | Uses IP addresses and port numbers for addressing, accommodating more devices & network flexibility |
Advantages and Applications | Simple, suitable for older systems with serial architecture | Faster transmission, flexibility for real-time communication, ideal for remote monitoring/control |
Data Transmission | Binary data transmission | Binary data converted to hexadecimal string |
Protocol Encapsulation | Uses MBAP message header | No CRC check code due to TCP reliability |
Communication Mode | Controller-to-controller and controller-to-device | Services between transport and network layers |
Transmission | Limited distance, slower speed | Longer distance, higher speed |
Usage | Industrial settings | Internet or local network environments |
Conclusion
Modbus RTU and Modbus TCP are prevalent in industrial automation. RTU leads, but TCP’s advantages are catching up. The decision relies on the discussed factors. Evaluate them to optimize system performance for your application.
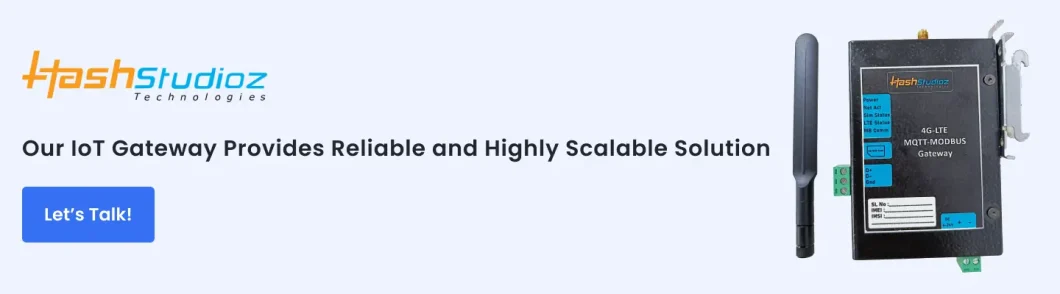
FAQ
1. Can I extend my 1.2 km RS-485 network?
Place an RS-485 repeater or an optically isolated repeater every 1.2 km to increase the RS-485 network’s range.
2. Can I use Rs485 to monitor more than 32 slaves?
The node range that our Modbus RTU supports is 0-255. To maintain proper communications, you might require RS-485 repeaters after 32 nodes (one master and 31 slaves). Several factors drive this, such as whether the RS485 transceivers have quarter-loading or full-loading.
3. How many slaves can connect using different protocols like RS232?
- There can only be one slave via RS-232.
- RS-485 can address up to 32 slaves.
- RS-422 can address up to 10 slaves.
4. Does the HashStudioz IoT gateway support RTU or TCP/IP?
HashStudioz IoT gateways are versatile and can support both RTU (Remote Terminal Unit) and TCP/IP (Transmission Control Protocol/Internet Protocol) communication protocols. These gateways facilitate communication between various devices and systems, adapting to different protocols commonly used in IoT environments.