The manufacturing industry has witnessed a remarkable transformation in recent years, evolving from labor-intensive manual processes to highly automated smart factories. This shift has been driven by advancements in IoT in Production, Artificial Intelligence Services, and Machine Learning Services. Today, smart factories leverage connected devices, sensors, and data analytics to enhance efficiency, productivity, and profitability. In this comprehensive guide, we explore how IoT in manufacturing industry is revolutionizing production, the benefits it offers, the challenges faced, and what the future holds for smart factories.
- Global IoT Market Growth: Expected to reach $1.39 trillion by 2030.
- Adoption Rate: 75% of manufacturers are adopting IoT technologies.
- Efficiency Gains: IoT-enabled factories report 20-30% improvement in productivity.
- AI and ML Integration: 50% of manufacturers use AI and ML for predictive maintenance.
Table of Contents
- What is IoT in Production?
- The Evolution of Manufacturing: From Manual to Smart Factories
- Key Technologies Powering Smart Factories
- Benefits of IoT in Manufacturing Industry
- Challenges in Implementing IoT in Manufacturing
- How to Implement IoT in Production: Step-by-Step Guide
- Future of Smart Factories
- Why Choose HashStudioz
- Conclusion
- FAQ’s
What is IoT in Production?
The Internet of Things (IoT) in Production is a cutting-edge technology that integrates interconnected sensors, devices, and systems within manufacturing environments to collect, exchange, and analyze data. It transforms traditional factories into smart factories by enabling real-time monitoring, predictive maintenance, and automated processes.
This interconnected ecosystem enhances operational efficiency, reduces downtime, and improves decision-making through data-driven insights. IoT in production forms the backbone of modern manufacturing, enabling seamless communication between machines, systems, and human operators.
Key Features of IoT in Production:
- Real-Time Data Monitoring:
- Tracks equipment performance and operational metrics in real time.
- Detects anomalies and prevents unexpected breakdowns.
- Remote Control:
- Allows operators to monitor and control machinery from remote locations.
- Ensures continuous production with minimal physical presence.
- Predictive Analytics:
- Utilizes Artificial Intelligence Services and Machine Learning Services to predict equipment failures and maintenance needs.
- Enhances equipment lifespan and reduces downtime.
- Automation:
- Reduces manual intervention by automating repetitive tasks.
- Minimizes errors, increases productivity, and improves product quality.
The Evolution of Manufacturing: From Manual to Smart Factories
Manufacturing has undergone a remarkable transformation, progressing from labor-intensive manual operations to highly automated and digitally connected smart factories. This evolution highlights humanity’s relentless pursuit of efficiency, precision, and innovation. Let’s delve into each stage:
1. Manual Era: The Foundation
- Characteristics:
- Relied heavily on human labor and craftsmanship.
- Processes were slow, error-prone, and lacked scalability.
- Minimal use of machines, leading to limited productivity.
- Challenges:
- High dependency on workforce availability.
- Quality control was inconsistent.
- Low production volumes and high operational costs.
2. Industrial Revolution: Mechanization and Efficiency
- Key Developments:
- Introduction of mechanized tools and steam-powered machinery in the late 18th and early 19th centuries.
- Transition from manual labor to machine-assisted processes.
- Establishment of assembly lines, enhancing mass production capabilities.
- Impact:
- Improved productivity and consistency.
- Lower production costs.
- Birth of modern manufacturing systems.
3. Automation Era: Precision and Control
- Technological Advancements:
- Emergence of Programmable Logic Controllers (PLCs) in the 20th century for automated processes.
- Adoption of robotics for repetitive tasks and precision assembly.
- Use of Computer Numerical Control (CNC) machines for accurate machining.
- Benefits:
- Increased reliability and efficiency.
- Reduced errors and downtime.
- Enhanced safety by minimizing human involvement in hazardous tasks.
4. Smart Factories: Intelligent Manufacturing
- Modern Innovations:
- Integration of IoT in production to enable real-time monitoring and control.
- Adoption of Artificial Intelligence Services for predictive analytics and quality assurance.
- Utilization of Machine Learning Services for process optimization and adaptive systems.
- Cloud computing for data storage and advanced analytics.
- Key Features:
- Connected Devices: Sensors and smart equipment communicate seamlessly.
- Data-Driven Operations: Real-time insights improve decision-making.
- Predictive Maintenance: Equipment health is monitored to prevent failures.
- Automation and Robotics: Robots perform tasks with minimal human intervention.
- Impact on Manufacturing Industry:
- Enhanced flexibility, scalability, and responsiveness.
- Significant reduction in downtime and operational costs.
- Improved sustainability through energy optimization and waste reduction.
This progression highlights the continuous pursuit of efficiency and innovation, with IoT in manufacturing industry playing a central role.
Key Technologies Powering Smart Factories
Artificial Intelligence Services: Artificial Intelligence (AI) is a cornerstone technology in smart factories, enabling advanced automation and intelligent decision-making. It empowers machines to:
- Analyze Data Patterns: AI detects anomalies, trends, and inefficiencies in production processes, ensuring continuous optimization.
- Automate Decision-Making: By processing real-time data, AI reduces reliance on human intervention, enhancing speed and accuracy.
- Enhance Quality Control: AI-powered image recognition identifies defects and inconsistencies in products, improving quality assurance and minimizing waste.
Machine Learning Services: Machine Learning (ML) complements AI by enabling systems to learn from data and improve performance over time. It supports:
- Predictive Maintenance: ML algorithms analyze equipment data to predict failures, allowing proactive maintenance and minimizing downtime.
- Demand Forecasting: Machine learning models predict inventory needs, optimizing stock levels and reducing excess storage costs.
- Process Optimization: ML fine-tunes workflows by identifying bottlenecks, improving resource utilization, and enhancing overall efficiency.
Benefits of IoT in Manufacturing Industry
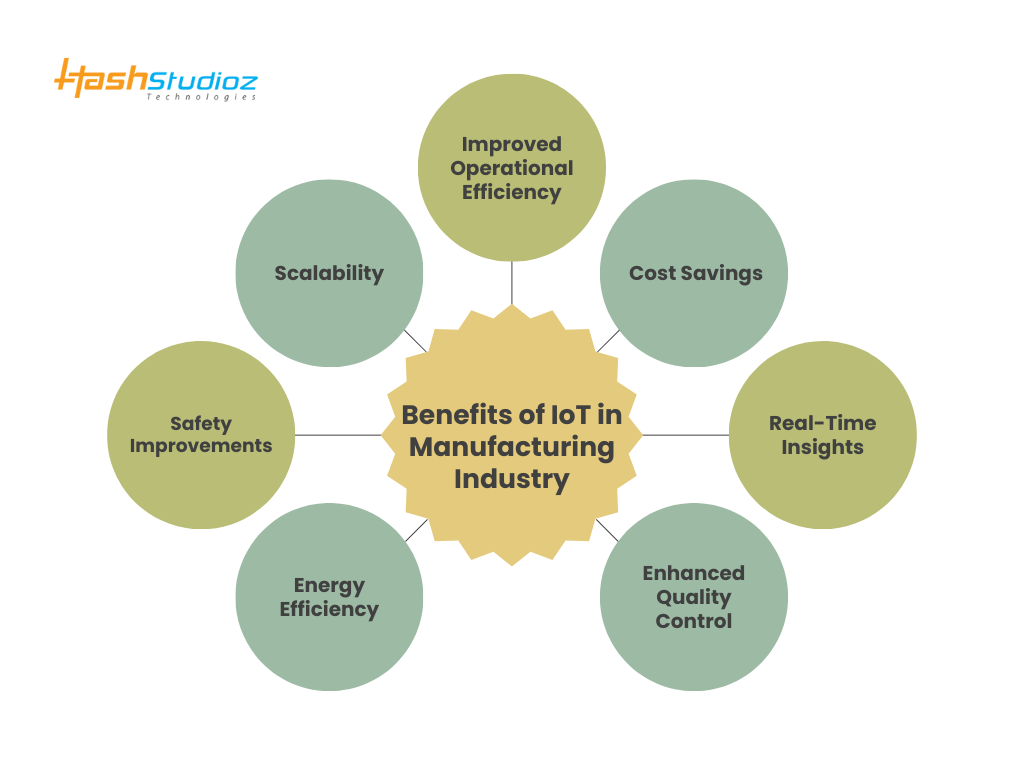
1. Improved Operational Efficiency: IoT automates workflows and optimizes production processes, minimizing manual interventions. Real-time monitoring of machines and systems reduces downtime, increases productivity, and ensures seamless operations across the manufacturing floor.
2. Cost Savings: With IoT-enabled predictive maintenance, manufacturers can detect equipment issues before they escalate, reducing repair costs and preventing costly downtime. Additionally, optimized resource utilization leads to long-term savings.
3. Real-Time Insights: IoT devices collect and analyze vast amounts of data, providing manufacturers with actionable insights. These insights enable faster and more accurate decision-making, enhancing operational strategies and resource allocation.
4. Enhanced Quality Control: Sensors and AI-powered analytics continuously monitor production quality. Any deviations are immediately flagged, ensuring defects are identified early, improving product consistency, and reducing wastage.
5. Energy Efficiency: IoT systems monitor energy consumption patterns and optimize usage, reducing waste and lowering energy costs. Smart systems also identify inefficiencies and suggest improvements for sustainable operations.
6. Safety Improvements: IoT solutions enhance workplace safety by tracking worker movements, monitoring hazardous environments, and providing alerts for potential risks. This reduces accidents and improves compliance with safety regulations.
7. Scalability: IoT solutions are highly scalable, enabling manufacturers to expand production lines, integrate new technologies, and adapt to changing market demands without overhauling existing systems.
Applications of IoT in Production
The Internet of Things (IoT) is revolutionizing the manufacturing industry by enabling smart, connected systems that improve efficiency, productivity, and cost-effectiveness. Below is a detailed breakdown of its key applications:
1. Asset Tracking and Management
Purpose:
- Monitors the location, condition, and performance of equipment and tools.
Benefits:
- Reduces equipment loss and theft.
- Tracks utilization rates for better resource allocation.
- Enhances equipment lifecycle management through real-time data insights.
2. Predictive Maintenance
Purpose:
- Prevents unexpected machine failures by predicting issues before they occur.
Benefits:
- Minimizes downtime by scheduling maintenance proactively.
- Lowers maintenance costs by addressing problems early.
- Extends equipment life through timely repairs.
3. Inventory Management
Purpose:
- Tracks raw materials, components, and finished goods in real time.
Benefits:
- Prevents stockouts and overstock situations.
- Automates replenishment processes.
- Improves warehouse operations and space utilization.
4. Energy Monitoring
Purpose:
- Monitors energy usage and optimizes consumption patterns.
Benefits:
- Reduces operational costs by identifying energy inefficiencies.
- Supports sustainability goals by minimizing waste.
- Ensures compliance with energy regulations.
5. Supply Chain Optimization
Purpose:
- Enhances logistics, transportation, and delivery processes.
Benefits:
- Provides end-to-end visibility into supply chains.
- Reduces delays and improves delivery accuracy.
- Streamlines order fulfillment and reduces operational risks.
6. Quality Assurance
Purpose:
- Ensures consistent product quality by monitoring production processes.
Benefits:
- Identifies defects early to minimize rework and waste.
- Maintains compliance with industry standards.
- Improves customer satisfaction with high-quality products.
7. Remote Monitoring and Control
Purpose:
- Enables operators to monitor and control manufacturing systems from remote locations.
Benefits:
- Enhances flexibility by allowing supervision from anywhere.
- Supports quick decision-making during emergencies.
- Enables centralized control over distributed production units.
Challenges in Implementing IoT in Manufacturing
Implementing IoT in manufacturing brings numerous advantages, but it also poses several challenges that organizations must address to achieve seamless integration and optimal performance. Below is a detailed overview of the key challenges:
1. High Initial Costs
Deploying IoT infrastructure requires a substantial upfront investment in hardware, software, connectivity, and cloud storage.
Key Challenges:
- Purchasing IoT-enabled devices and sensors.
- Setting up robust networks and servers for real-time data processing.
- Customizing existing systems to integrate IoT technologies.
Impact:
Small and medium-sized manufacturers may face budget constraints, making IoT adoption difficult without external funding or government incentives.
2. Data Security Risks
IoT systems are highly interconnected, making them attractive targets for cybercriminals.
Key Challenges:
- Vulnerability to hacking, malware, and ransomware attacks.
- Risks associated with data breaches, compromising sensitive information.
- Ensuring compliance with data protection regulations.
Impact:
Manufacturers need to implement advanced cybersecurity measures, such as encryption, firewalls, and intrusion detection systems, to safeguard their IoT networks.
3. Integration Complexity
Many manufacturers operate legacy systems that may not be compatible with modern IoT technologies.
Key Challenges:
- Replacing or upgrading outdated equipment to support IoT solutions.
- Ensuring seamless communication between old and new systems.
- Managing downtime during the transition.
Impact:
Integrating IoT with legacy systems can increase implementation time and costs, requiring careful planning and phased deployment strategies.
4. Skills Gap
The adoption of IoT in manufacturing demands specialized expertise in areas like data analytics, cybersecurity, and system integration.
Key Challenges:
- Shortage of skilled professionals to design, deploy, and maintain IoT systems.
- Need for continuous training to keep up with evolving technologies.
- High competition for experienced IoT engineers and data scientists.
Impact:
Manufacturers must invest in employee training programs or collaborate with external Artificial Intelligence Services and Machine Learning Services providers to address the skills gap.
5. Data Overload
IoT systems generate massive volumes of data, which can overwhelm manufacturers if not managed effectively.
Key Challenges:
- Collecting and storing data securely.
- Analyzing data in real time to extract actionable insights.
- Avoiding data silos and ensuring data accessibility across departments.
Impact:
Businesses must adopt advanced data analytics and AI tools to process and interpret data efficiently, enabling better decision-making and performance optimization.
How to Implement IoT in Production: Step-by-Step Guide
1. Assess Business Needs: Begin by identifying your business goals and pain points. Understand the specific areas where IoT can provide improvements, such as operational efficiency, maintenance, or quality control.
2. Plan Infrastructure: Choose the appropriate hardware (sensors, actuators, devices) and software (IoT platforms, analytics tools) based on your business needs. Ensure scalability and compatibility with existing systems.
3. Integrate Technologies: Connect the various sensors, devices, and systems to create a seamless network. Ensure interoperability between the IoT devices and your production equipment for smooth data flow and control.
4. Data Management: Establish a robust system for data collection, storage, and analysis. Use IoT platforms to gather real-time data and analytics tools to process and derive actionable insights.
5. Testing and Optimization: Run pilot tests to evaluate the performance of the IoT systems. Identify areas for improvement and optimize the setup to ensure reliability and efficiency before full-scale deployment.
6. Employee Training: Provide training to employees on how to operate, monitor, and maintain IoT systems. Ensure they understand the value of IoT and how to use the new tools effectively.
7. Continuous Monitoring: After deployment, continuously monitor the IoT systems to evaluate performance. Use the insights to make ongoing improvements, address issues, and adapt to changing business needs.
Future of Smart Factories
The future of smart factories is defined by the deeper integration of Artificial Intelligence (AI), Machine Learning (ML), and Internet of Things (IoT) technologies. These advancements promise to revolutionize production processes, making them more efficient, agile, and sustainable. Key trends shaping the future of smart factories include:
1. Digital Twins: Virtual replicas of physical systems will be created to simulate, analyze, and optimize production processes in real time. This allows manufacturers to anticipate issues and make improvements before implementing changes on the factory floor.
2. Edge Computing: With edge computing, data will be processed closer to its source, reducing latency and enabling faster decision-making. This technology enhances the real-time capabilities of smart factories, allowing for immediate responses to production challenges.
3. 5G Connectivity: The introduction of 5G will provide factories with faster, more reliable data transmission, enabling seamless communication between IoT devices and systems, and supporting real-time data analytics and automation.
4. Sustainability: Future smart factories will focus on eco-friendly practices, such as reducing energy consumption, minimizing waste, and using renewable resources. Sustainability will be a key priority as manufacturers seek to align with global environmental goals.
Why Choose HashStudioz
HashStudioz is a trusted leader in IoT solutions for manufacturing, offering tailored, scalable, and secure services that optimize production and improve efficiency. With expertise in AI, Machine Learning, and IoT, they provide innovative solutions to transform your factory into a smart, sustainable environment.
How HashStudioz Can Help You
HashStudioz enhances operational efficiency by automating processes, enabling real-time insights, and reducing downtime with predictive maintenance. Their solutions also improve quality control, streamline supply chain management, and optimize energy usage, all while integrating seamlessly with your existing systems.
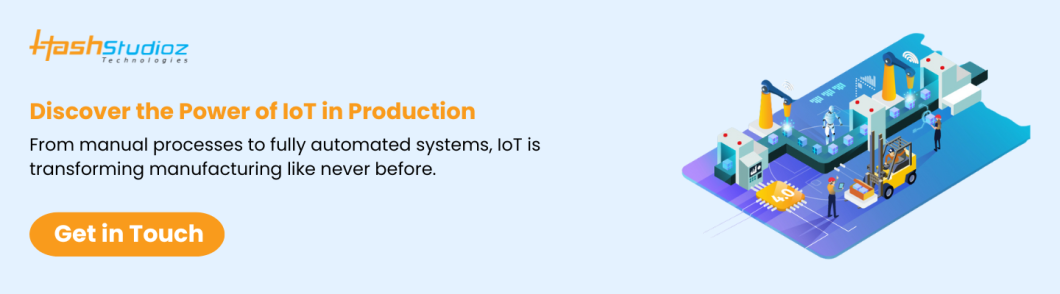
Conclusion
The transition from manual processes to smart factories marks a revolutionary shift in the manufacturing industry. IoT in Production is the driving force behind this transformation, enabling efficiency, cost savings, and enhanced quality. By leveraging Artificial Intelligence Services and Machine Learning Services, manufacturers can optimize their operations and remain competitive in a rapidly evolving landscape.
As technology continues to advance, the potential for IoT in manufacturing industry will only grow, paving the way for smarter, more sustainable factories.
FAQ’s
What is IoT in Production?
IoT in production involves using interconnected devices to collect and analyze data, improving manufacturing processes.
How does AI contribute to smart factories?
AI enhances decision-making, quality control, and predictive maintenance in smart factories.
What are the challenges of implementing IoT in manufacturing?
Challenges include high initial costs, data security risks, and integration complexities.
How can manufacturers get started with IoT?
Begin by assessing needs, planning infrastructure, integrating technologies, and training employees.
What is the future of IoT in manufacturing?
The future includes advancements like digital twins, edge computing, and sustainable practices.