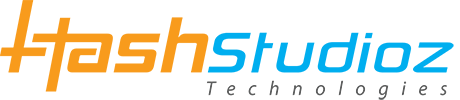
- About Us
- Our Services
- Solution
- Products
- Hire
- Technologies
- Industries
- Resources
- Contact Us
The case study examines the deployment of a customized validation kit for fluid valve electrical (DAIT) and mechanical parameter collection to improve product quality assurance and longevity.
An industry leader with over 80 years of industry expertise, specializing in a wide array of high-quality pneumatic and fluid control products. They were seeking a comprehensive solution to measure and validate both electrical and mechanical parameters of their large fluid valves for quality assurance and performance optimization.
We designed a validation kit equipped with several key features to meet our objectives:
Accurate measurement and recording of parameters ensured the integrity of collected data, enhancing subsequent analyses' reliability.
The complete PCB design with user-serviceable parts added flexibility, allowing for convenient maintenance and adaptability to evolving validation needs.
The implementation of a simple one-touch application activation feature ensured a user-friendly interface, simplifying users' operational experience.
The comprehensive yet cost-effective hardware and software solution provided the necessary functionalities without exceeding budgets.
Aluminum-enclosed hardware, with an inbuilt power supply, made valve testing efficient and accurate, contributing to a thorough validation.
The application seamlessly recorded data associated with valve serial numbers and parameter status, creating a comprehensive and well-organized dataset.
Exporting data to an Excel sheet allowed for simplified reporting and analysis, aiding in quick decision-making and troubleshooting.