Manufacturers today have a growing reliance on software solutions to optimize operations, improve product quality, and streamline production processes. However, when it comes to choosing the right type of manufacturing software, companies must decide between custom-built solutions and off-the-shelf systems. Each choice has its advantages and challenges, depending on the specific needs of the business. This article compares both, helping you decide which option fits your company’s goals.
Table of Contents
- What Is Custom Manufacturing Software?
- What Are Off-the-Shelf Solutions?
- Cost Analysis: Custom vs. Off-the-Shelf
- Technical Fit: Aligning with Manufacturing Processes
- Scalability and Flexibility
- Integration with Existing Systems
- Security and Compliance
- Implementation Timeframe
- Why Choose HashStudioz for Your Custom Manufacturing Software Needs?
- Conclusion
- Frequently Asked Questions (FAQ)
- 1. What is the main difference between custom manufacturing software and off-the-shelf solutions?
- 2. Is custom manufacturing software more expensive than off-the-shelf solutions?
- 3. How long does it take to implement custom manufacturing software compared to off-the-shelf solutions?
- 4. Can off-the-shelf software be customized to meet my business needs?
- 5. Which option is better for scalability and future growth?
What Is Custom Manufacturing Software?
Developers create custom manufacturing software from scratch to meet a specific manufacturing business’s unique needs. The solution integrates seamlessly into existing workflows, including proprietary machines, processes, and data sources. It ensures flexibility to adapt as production needs evolve. Additionally, custom solutions align with specific industry requirements, offering a tailored experience that enhances efficiency and compliance.
A Manufacturing Software Development Company works closely with your team to design, implement, and maintain custom software that matches the exact specifications of your business processes. This collaborative approach ensures that the software is not only functional but also optimized for the unique challenges of your production environment.
What Are Off-the-Shelf Solutions?
Off-the-shelf manufacturing software includes ready-made tools developed for a wide range of industries and processes. Companies can purchase or subscribe to these systems immediately. They offer standard features like inventory management, scheduling, and order processing, and teams can deploy them quickly. However, these solutions often fail to align perfectly with specific business needs, leading to necessary adjustments or compromises in process handling.
While off-the-shelf software offers cost advantages and faster deployment, it often falls short in meeting complex or highly specialized requirements. Some degree of customization exists, but vendors generally limit it and restrict the ability to modify or extend software features.
Cost Analysis: Custom vs. Off-the-Shelf
1. Custom Software Costs
- Higher Initial Investment: Custom software requires significant upfront costs for requirement analysis, design, coding, testing, and deployment. This is due to the involvement of developers, project managers, QA testers, and integration specialists. Although the development cost is high, it’s justified by the precision and efficiency it brings to a business’s unique manufacturing processes.
- Tailored Cost Efficiency Over Time: Although expensive initially, custom solutions reduce costs over time. They eliminate unnecessary features, reduce process redundancies, and enhance productivity. By automating manual tasks and supporting complex operations, businesses see improved throughput and return on investment. Over the long term, this results in savings that often surpass the initial investment.
- Ongoing Maintenance Based on Needs: Maintenance of custom software includes regular updates, performance improvements, and system scalability. Companies can choose in-house IT teams or a Manufacturing Software Development Company to manage this. Control over update frequency and features ensures minimal disruption and tailored functionality, allowing businesses to optimize based on actual usage.
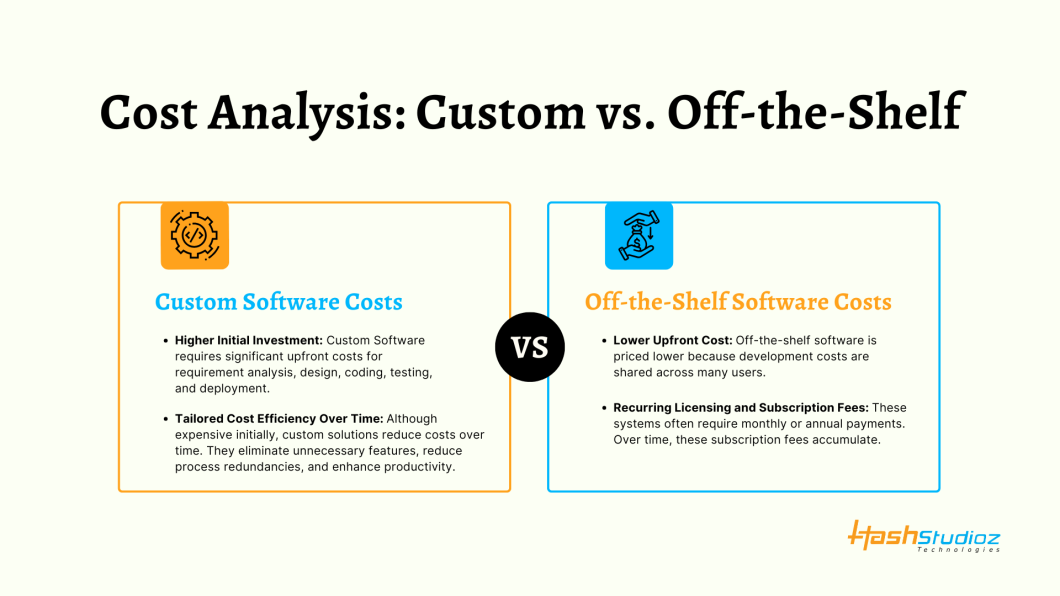
2. Off-the-Shelf Software Costs
- Lower Upfront Cost: Off-the-shelf software is priced lower because development costs are shared across many users. Businesses can buy a license or subscribe to use it, with minimal initial expenses. This makes it attractive for small manufacturers with basic needs or limited budgets, though not always the most efficient long-term option.
- Recurring Licensing and Subscription Fees: These systems often require monthly or annual payments. Over time, these subscription fees accumulate. Additional costs may apply for user seats, feature upgrades, or cloud storage. While the startup expense is low, long-term costs may rival or exceed that of a custom solution, especially for large-scale operations.
- Additional Costs for Customization: Most off-the-shelf systems allow limited customization, which may not be enough for unique manufacturing workflows. Any serious customization or third-party integration often requires additional investment. This can lead to higher costs, particularly if you need support for legacy systems, custom dashboards, or niche production modules.
Technical Fit: Aligning with Manufacturing Processes
1. Custom Software
- Designed for Specific Workflows: Custom solutions align precisely with how your factory operates. From job routing and production planning to equipment interfacing, the system is built around your specific methods. This ensures minimal changes to existing operations and results in faster user adoption, fewer workarounds, and better overall system performance.
- Advanced Functionalities: Custom-built systems can integrate advanced tools like machine learning for predictive maintenance, IoT for live monitoring, and AI for production optimization. These features enhance control and enable smarter decision-making. With flexibility in architecture, manufacturers gain an edge in automation and real-time analytics.
- Real-Time Data Integration: The system collects and synchronizes data from machines, PLCs, sensors, and ERP systems in real time.
- This helps maintain production continuity and accurate reporting. Custom solutions ensure that all systems talk to each other without data duplication or lag, improving process control and business intelligence.

2. Off-the-Shelf Software
- Generalized Features: These systems are developed to serve a wide range of industries. Their features work for most standard manufacturing setups but fall short when dealing with specialized or non-standard processes. Manufacturers might need to change how they operate to fit the software, which can lead to process inefficiencies.
- Limited Support for Custom Machines or Workflows: Integration with legacy equipment or non-standard operations can be difficult. Many systems only support modern or widely used platforms. If your operations include unique hardware or niche software, integration can become time-consuming and expensive, requiring middleware or third-party plugins.
- Feature Gaps Without Custom Modules: Many off-the-shelf platforms lack high-end features like smart inventory alerts, equipment learning models, or custom KPI dashboards. Without these, manufacturers either adjust their expectations or pay more for premium modules that might still not fully match their needs.
Scalability and Flexibility
1. Custom Software:
Custom software is highly scalable. It is designed with the future growth of your business in mind. As your manufacturing processes become more complex or expand to new product lines, custom software can evolve to meet new requirements. Adding new modules, integrating additional machines, or adjusting features to accommodate changes is much easier with a tailored solution. You have the flexibility to adapt the software’s features to suit your company’s strategic goals without being limited by vendor roadmaps.
This scalability ensures that the software can grow alongside your business, providing a long-term solution that doesn’t require switching systems as your needs change. Furthermore, custom software allows for more granular control over performance optimization and feature expansion.
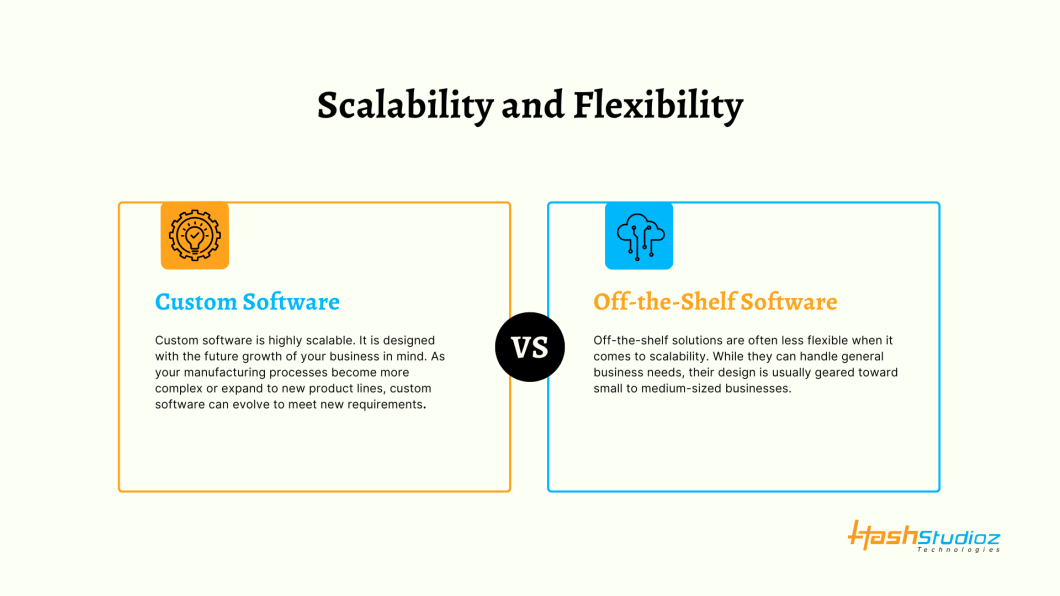
2. Off-the-Shelf Software:
Off-the-shelf solutions are often less flexible when it comes to scalability. While they can handle general business needs, their design is usually geared toward small to medium-sized businesses. As your operations grow or require more specialized capabilities, you may find that the software does not scale easily or that the vendor’s future updates do not meet your evolving needs.
To scale an off-the-shelf solution, you may need to upgrade to a higher-tier plan or purchase additional modules, both of which could lead to rising costs. In some cases, you may even outgrow the solution entirely and have to switch to another system, leading to additional migration costs and disruption.
Data Lake Consulting Services Explained: Benefits, Challenges & Use Cases
Integration with Existing Systems
1. Custom Software:
Developers build custom solutions to meet the specific needs of your existing infrastructure. You can easily integrate them with your Enterprise Resource Planning (ERP) systems, Manufacturing Execution Systems (MES), sensors, and other industrial automation tools your company uses. This ensures a seamless flow of data across various departments, from production to inventory management to sales, improving decision-making and reducing data errors.
The ability to integrate custom-built software with unique machines or specialized data collection systems is a significant advantage. Additionally, as your software evolves, it can continue to integrate with emerging technologies, ensuring that your operations remain interconnected and efficient.
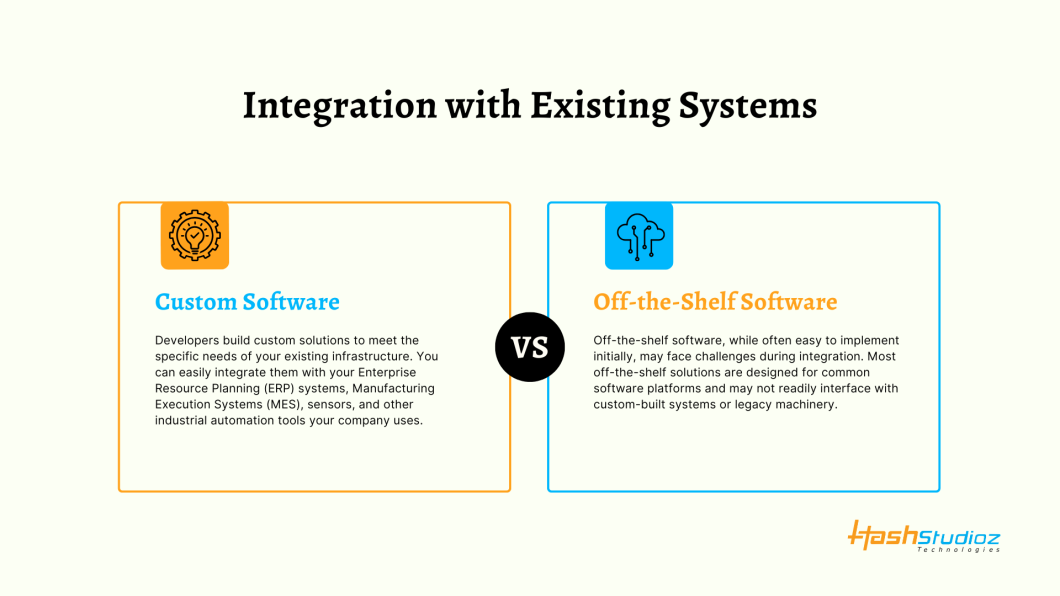
2. Off-the-Shelf Software:
Off-the-shelf software, while often easy to implement initially, may face challenges during integration. Most off-the-shelf solutions are designed for common software platforms and may not readily interface with custom-built systems or legacy machinery. Integration could require third-party middleware, custom scripts, or additional tools to ensure smooth data exchange, which can increase costs and create inefficiencies.
In some cases, the integration process might disrupt operations or create data silos, where information is not shared properly between systems. Over time, this can lead to increased manual work and errors that affect overall productivity.
Security and Compliance
1. Custom Software:
Custom manufacturing software allows businesses to implement specific security protocols that meet their individual risk profiles. You can control data access levels, encryption methods, and monitoring systems to protect your proprietary data and intellectual property. Additionally, developers can design custom solutions to comply with industry-specific standards, such as ISO certifications or FDA regulations, helping you pass audits and meet regulatory requirements.
Custom-built software also gives you greater control over updates and patches, allowing your team to fix vulnerabilities quickly and thoroughly.
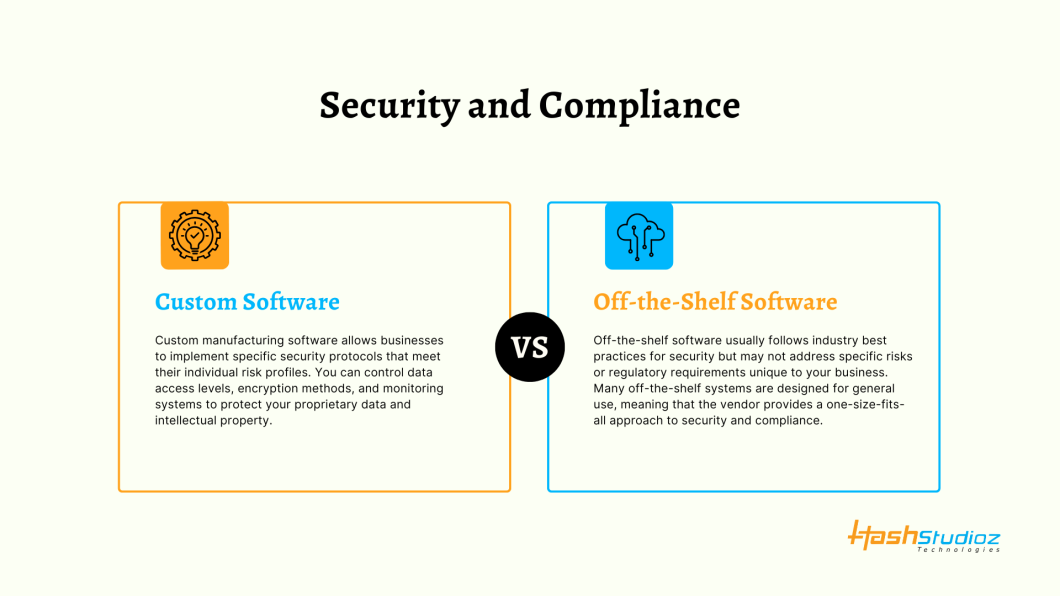
2. Off-the-Shelf Software:
Off-the-shelf software usually follows industry best practices for security but may not address specific risks or regulatory requirements unique to your business. Many off-the-shelf systems are designed for general use, meaning that the vendor provides a one-size-fits-all approach to security and compliance. Customizing security settings or ensuring compliance with niche regulations may be difficult or costly.
Data privacy and security may also be a concern if the software is cloud-based, as sensitive data could be stored outside of your control. This might raise issues in industries with stringent data protection requirements.
Implementation Timeframe
1. Custom Software:
The development of custom software is a lengthy process, usually taking several months to a year, depending on the complexity of the requirements. It involves multiple phases such as design, development, testing, and deployment. The process is highly collaborative, ensuring that the final product meets all of your business’s specific needs. Although implementation takes longer than off-the-shelf solutions, the process creates a finely tuned software system that fits your operations perfectly.
During implementation, the Manufacturing Software Development Company will work closely with your team to ensure proper training and support, which can ease the transition to the new system.
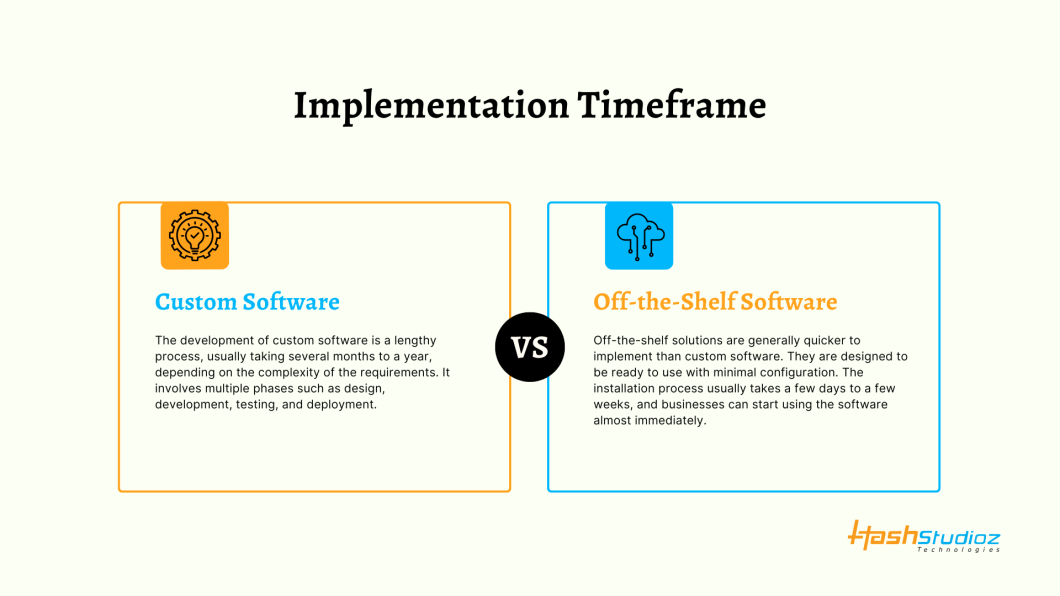
2. Off-the-Shelf Software:
Off-the-shelf solutions are generally quicker to implement than custom software. They are designed to be ready to use with minimal configuration. The installation process usually takes a few days to a few weeks, and businesses can start using the software almost immediately. However, the time spent on training, configuration, and minor customizations can extend the overall deployment period.
Why Choose HashStudioz for Your Custom Manufacturing Software Needs?
If your manufacturing business needs a highly specialized, tailored solution, HashStudioz can be your ideal partner. With years of experience in developing custom manufacturing software, HashStudioz offers comprehensive services from design to implementation and ongoing support.
Whether you need to optimize production processes, integrate advanced technologies, or ensure compliance with industry standards, HashStudioz delivers bespoke software that adapts to your business goals and scales with your growth.
Ready to take your manufacturing operations to the next level?
Contact HashStudioz today for a consultation and let us build the perfect software solution for your unique business needs.
Conclusion
Choosing between custom manufacturing software and off-the-shelf solutions depends on your business’s specific needs. While off-the-shelf systems offer lower upfront costs and faster implementation, they may lack the flexibility, scalability, and integration capabilities of custom solutions. For manufacturers with complex processes or unique requirements, custom software is often the best choice, providing long-term value and greater control.
Ultimately, the decision should be based on the size of your operation, the complexity of your manufacturing processes, and your long-term goals. By carefully evaluating your requirements and collaborating with an experienced Manufacturing Software Development Company, you can ensure that you choose the right software solution for your business.
Frequently Asked Questions (FAQ)
1. What is the main difference between custom manufacturing software and off-the-shelf solutions?
Custom manufacturing software fits your business needs and integrates with your processes, systems, and equipment.It offers flexibility to adapt as your business grows and evolves. On the other hand, off-the-shelf solutions are ready-made software that cater to a broad range of industries and processes, with limited customization options.
2. Is custom manufacturing software more expensive than off-the-shelf solutions?
Yes, custom software typically involves higher initial costs due to the development, design, and deployment phases. However, the long-term value can outweigh the initial investment, as it is tailored to optimize your unique operations and reduce inefficiencies. Off-the-shelf software, while cheaper upfront, may incur additional costs for customization, licensing, and recurring fees over time.
3. How long does it take to implement custom manufacturing software compared to off-the-shelf solutions?
Custom software development can take several months to a year, depending on the complexity of your requirements. It involves a detailed design and development process to ensure the solution meets your specific business needs. Off-the-shelf software, however, can be implemented much faster, usually within days or weeks, though additional time may be required for training and minor customizations.
4. Can off-the-shelf software be customized to meet my business needs?
Off-the-shelf software typically offers some level of customization, but it is limited. Deeper customizations for unique processes or legacy systems often need third-party tools. These can add cost and complexity. Basic tweaks like UI or feature changes are easier.
5. Which option is better for scalability and future growth?
Custom manufacturing software is highly scalable, designed with the flexibility to grow alongside your business. As your operations expand or change, the system can be modified to accommodate new requirements, ensuring long-term sustainability. Off-the-shelf solutions are less flexible and may require upgrades or additional modules to meet your growing needs, which could be costly or inefficient in the long term.